
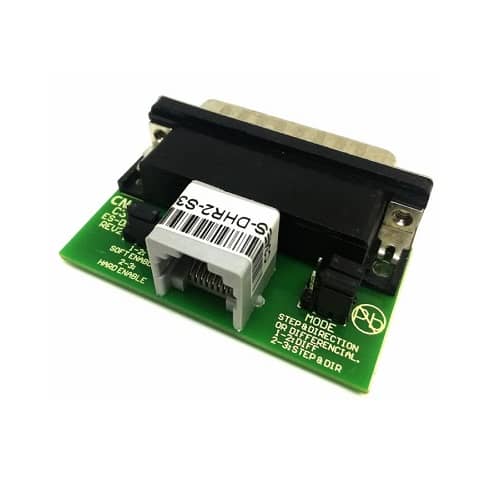
Grippers can be either electric servo grippers or pneumatic grippers. The assembly consists of the channel relays, stepper motor drivers, one for each motor controlled by an Arduino Mega Micro-controller.Ī kill switch is installed on the top of the box to abort during an emergency or to kill power. The electronic control assembly is encased in an electrical enclosure box. The arm uses 6 Stepper motors and a separate motor for the track linear movement. The Jacobian matrix helps define a relationship between the robot’s joint parameters and the end-effector velocities. Once the robot’s joint angles are calculated using the inverse kinematics, a motion profile can be generated using the Jacobian matrix to move the end-effector from the initial to the target pose. The robot configuration is a list of joint positions that are within the position limits of the robot model and do not violate any constraints the robot has. The grasping end of a robot arm is designated as the end-effector. For example, to perform automated bin picking, a robotic arm used in a manufacturing line needs precise motion from an initial position to the desired position between bins and manufacturing machines. Inverse kinematics is the use of kinematic equations to determine the motion of a robot to reach the desired position. Kinematics is the study of motion without considering the cause of the motion, such as forces and torques. The Robot is designed in such a way that it can be 3D printed and it can be manufactured in Aluminium. The AR2 is a multipurpose six-axis robotic gripper arm that can be programmed to perform various activities. The AR2 is an open source project by Chris Annin which was uploaded to YouTube and GitHub.
